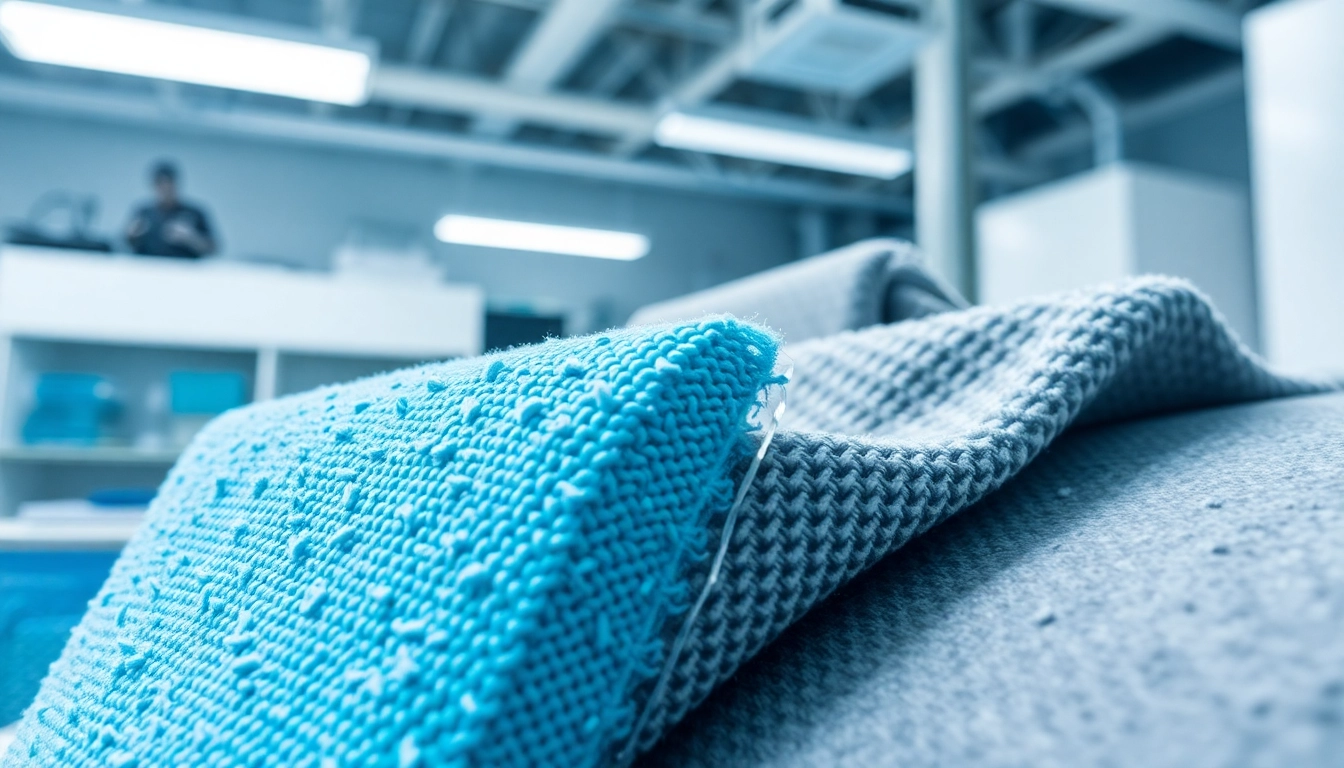
Understanding Thermal Management Materials
In the fast-evolving landscape of electronics, thermal management materials play a pivotal role in ensuring device efficiency and longevity. These materials are specifically designed to manage and dissipate heat generated by electronic components, thus safeguarding against overheating and enhancing performance. Effective thermal management is crucial in a variety of applications, from smartphones and laptops to industrial machinery and automotive systems. In this context, understanding thermal management materials is fundamental for engineers, designers, and manufacturers aiming to optimize their products.
What are Thermal Management Materials?
Thermal management materials encompass a broad range of substances designed to enhance heat dissipation and thermal performance in electronic systems. They can either conduct heat away from sensitive components or provide insulation to maintain optimal operating temperatures. Various materials serve this purpose, including thermal interface materials (TIM), adhesives, gels, gap fillers, phase change materials, and heat spreaders.
Importance of Thermal Management in Electronics
The increasing demand for compact, powerful electronics has made thermal management more critical than ever. As devices become smaller and more powerful, the amount of heat generated per unit area increases. This challenges engineers to implement effective thermal solutions that prevent thermal build-up, which can result in degraded performance, reduced lifespan, and potential failure of components. For instance, in the automotive industry, failure to manage heat can cause critical systems to malfunction, leading to unsafe conditions. Therefore, engineers must prioritize thermal management in the design phase to enhance reliability and efficiency.
Types of Thermal Management Materials
There are several types of thermal management materials, each engineered for specific applications and requirements. Understanding these materials and their properties is essential for selecting the right solution for a given scenario.
- Thermal Interface Materials (TIM): These serve as a bridge between heat-generating components and heat sinks or other thermal management systems, enhancing thermal transfer by filling microscopic gaps between surfaces.
- Phase Change Materials (PCMs): These materials absorb and release thermal energy as they change from solid to liquid and vice versa, allowing for efficient heat regulation.
- Gap Fillers: Soft, conformable materials that are used to fill spaces between heat sources and heat dissipators, ensuring even heat distribution.
- Thermal Adhesives and Tapes: These provide robust bonds while also facilitating effective heat transfer, making them ideal for mounting components.
- Heat Spreaders: Often composed of materials with high thermal conductivity, these components distribute heat away from hot spots to prevent overheating.
Types of Thermal Interface Materials (TIM)
Different Categories of TIM
Thermal Interface Materials can be categorized into several primary types based on their composition and function:
- Thermal Pastes: These are viscous substances applied between surfaces to enhance heat conduction. Commonly used in high-performance CPUs and GPUs, pastes fill air gaps and provide excellent thermal conductivity.
- Thermal Pads: These are solid materials that provide a simple installation process and moderate thermal performance. Thermal pads are often used where ease of application and removal is valued.
- Thermal Greases: Similar to pastes but often used in applications with lower thermal demands, greases can be silicone-based or non-silicone based, affecting their performance and application suitability.
- Self-adhesive Films: These combine adhesive properties with thermal conduction, simplifying the assembly of heat sinks to devices while ensuring effective heat transfer.
Performance Metrics of Thermal Interface Materials
When evaluating Thermal Interface Materials, several key performance metrics should be considered:
- Thermal Conductivity: This is the primary measure of a material’s ability to conduct heat. Higher thermal conductivity values indicate better performance.
- Thickness: The thickness of TIM can affect thermal performance. Thinner materials are beneficial up to a point, as they can create tighter contact between surfaces.
- Viscosity: This affects the application process of pastes and greases. A suitable viscosity allows for easy application while ensuring that the material fills gaps effectively.
- Operational Temperature Range: Understanding the temperature limits of TIM is essential to ensure compatibility with the operating conditions of the application.
- Compressibility: This affects how well TIM fills gaps under pressure and helps maintain contact under thermal expansion or mechanical movement.
Choosing the Right TIM for Your Project
Selecting the appropriate Thermal Interface Material involves analyzing several factors:
- Application Requirements: Consider the specific heat generation rates and thermal pastes that will be used in your design.
- Cost vs. Performance: Evaluate the trade-offs between cost and performance metrics, ensuring that the selected TIM meets thermal management needs without exceeding budget constraints.
- Ease of Application: Depending on production methods, select materials that can be easily appliqued, whether they are greases, tapes, or pads.
- Compatibility: Ensure that the material is compatible with the other components in terms of chemical interaction and thermal behavior.
Applications of Thermal Management Materials
Common Uses in Electronics
Thermal management materials are widely utilized in various electronic devices, helping to handle heat dissipation efficiently:
- Computers: CPUs and GPUs are often equipped with thermal pastes to maintain optimal operating temperatures.
- Smartphones: These devices benefit from thermal pads and gap fillers that prevent overheating during intensive operations.
- LED Lighting: The heat generated by LEDs necessitates the use of thermal interface materials to prolong the lifespan and efficiency of lighting systems.
- Automotive Applications: Thermal management materials are critical in electric vehicles to regulate battery and engine temperatures.
Innovative Solutions in Heat Management
The quest for better thermal management continues to inspire innovative solutions. These include:
- Advanced Materials: Researchers are developing new composites, such as graphene and carbon nanotube-based materials, to enhance thermal conductivity.
- Embedded Cooling Technologies: Innovations such as micro-channel cooling in PCBs emphasize direct cooling at the source, capitalizing on advanced manufacturing techniques.
- Active Cooling Systems: Products that employ thermoelectric devices for real-time temperature management are being integrated into various applications.
Case Studies: Success Stories
Several industries have benefited notably from advanced thermal management strategies:
- Consumer Electronics: A leading smartphone manufacturer implemented a new thermal interface material that improved heat dissipation in their flagship model, enhancing performance during gaming and high-definition video playback.
- Electric Vehicles: A major automotive company utilized phase change materials in their batteries, resulting in better temperature regulation under various driving conditions, ultimately enhancing vehicle safety and reliability.
- Data Centers: By adopting thermal management materials that align with high-demand servers, a large data center reduced cooling costs by 30%, demonstrating significant savings over time.
Best Practices for Implementing Thermal Materials
Installation Tips for Effective Heat Transfer
Getting the installation process right is crucial for maximizing the effectiveness of thermal management materials:
- Surface Preparation: Ensure that the surfaces are clean and free of contaminants. This facilitates better contact and heat transfer.
- Application Techniques: Follow manufacturer guidelines for applying TIM or pads, ensuring the right thickness and distribution.
- Secure Mounting: Ensure that the components are firmly mounted to maintain contact after installation, especially as devices heat up and cool down.
Maintenance and Monitoring of Thermal Solutions
Regular maintenance and monitoring will ensure the longevity and efficiency of thermal management systems:
- Regular Inspections: Check for any signs of wear or degradation in materials, especially in high-usage applications.
- Temperature Monitoring: Implement temperature sensors to track performance over time, ensuring that heat levels stay within acceptable parameters.
- Replacement Schedule: Establish a maintenance schedule for replacing TIM to maintain optimal performance, especially after prolonged use in demanding conditions.
Evaluating Performance Post-Implementation
Post-implementation evaluation is essential to assess the effectiveness of thermal management solutions:
- Temperature Mapping: Use thermal imaging technologies to identify hot spots and assess the performance of thermal materials.
- Performance Metrics: Compare thermal performance against benchmarks to ensure that the installed materials meet expected standards.
- Feedback Loops: Collect data from users to improve future iterations of thermal solutions based on real-world applications and performance.
The Future of Thermal Management Solutions
Emerging Technologies in Thermal Materials
The future of thermal management will be shaped by advancements in material science and engineering:
- Nanotechnology: The use of nanoscale materials promises enhanced thermal conductivity, leading to thinner and more efficient heat management solutions.
- Smart Materials: Developments in materials that can change properties in response to temperature changes offer new possibilities for adaptive thermal management.
- Integration with Digital Technologies: Future thermal management systems may integrate with IoT devices for real-time monitoring and automated adjustments.
Trends Shaping the Industry
Several overarching trends are influencing the thermal management market landscape:
- Sustainability Initiatives: There is a push for environmentally friendly materials and methods in thermal management, promoting sustainable manufacturing practices.
- Miniaturization: As devices continue to shrink, the demand for space-efficient thermal solutions that maintain efficacy is increasing.
- Increased Collaboration: Partnerships between material manufacturers, electronics companies, and academic institutions are fostering innovation and accelerating development times.
Looking Ahead: Innovations on the Horizon
The future of thermal management materials looks promising, with many innovations on the horizon. Enhanced computational modeling for heat transfer is expected to lead to the development of tailored materials that optimize thermal performance in real-time. Additionally, the integration of advanced manufacturing techniques such as 3D printing offers exciting potential for crafting custom thermal solutions tailored to specific needs and applications.